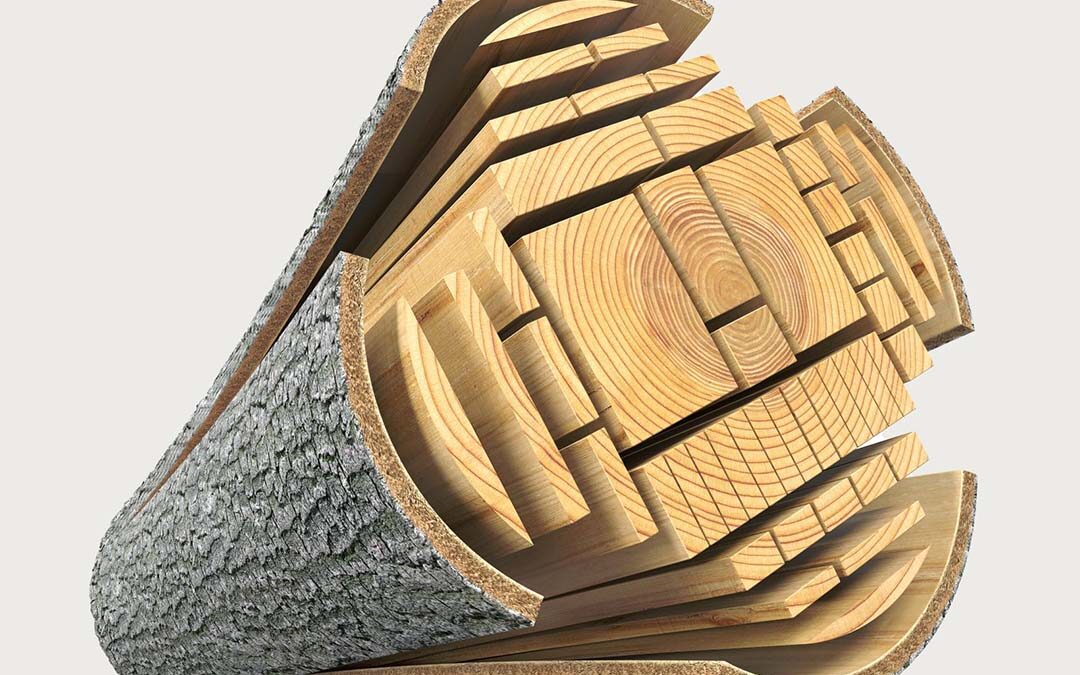
Wood For Making Furniture
Every project starts roughly the same. You need something and think to yourself, I can make that. You sit down, pencil in hand, and sketch your ideas. With the rough idea in hand, you make a quick cut list to figure out just how much, and what kinds of materials you’ll need. The next step is to then take a moment to get over the shock of how much the material is going to cost. Undeterred you decide to push on, but you’ve got some decisions to make. In this article, we’ll go over some of my thoughts on materials and the many things to consider before you begin that next masterpiece.
Choosing the right materials for any project is the first and arguably the most important step in a successful project. If you make good decisions and choose wisely, not only will the outcome of your next project be improved, but the overall experience will be much more enjoyable. Things such as durability, strength, aesthetics, color, workability, cost, stability, and availability, are all things to keep in mind when choosing the right material for each specific project. By carefully considering all these factors, you can make an informed decision and by the time you’ve completed your project, you’ll have a piece that will stand up to the test of time.
So, you have a design, you have a cut list, and you have a vision. Where to start? Take a moment to consider what it is you are building and your desired outcome. Pieces of fine furniture will require a large investment of both time and money. Using the finest materials is likely to be the best approach. On the other hand, you’re not likely to use furniture grade on that new chicken coop. Sometimes cheap lumber from the big box store and quick and easy joinery is the way to go.
Ok, first things first.
Wood movement, yes, it’s real, and it can cause havoc. If you’re designing your pieces of furniture, make sure to allow for this, and never underestimate the amount of movement and the destructive nature it can have if not allowed to move freely. I mention this because it will play a large role in the woods you choose for a particular project. Take some time and learn about wood movement and how it differs, sometimes extremely, from species to species. Years ago in college, we were introduced to the book “Understand Wood – A craftsman’s guide to wood technology” by Bruce Hoadley. Although printed over 40 years ago it remains a book, I’d recommend looking at.
Of course, there’s endless information available online and time spent educating yourself in this area will pay dividends later when your choosing appropriate woods for specific designs. You’ll also have a good understanding of why certain craftsmen choose specific woods for their designs and why some pieces of furniture fail while others seem to last forever.
For this article let’s assume we’re going to make the Branch Butchers Trestle Table. After taking some time to familiarize yourself with the design, consider your budget, and think about the desired outcome you decide you’re all in, and you’re going to use some high-grade materials. Before you go head out to the local lumber supplier and load up your vehicle and empty your wallet let’s consider what species would be best. Your new table will have different requirements than a coffee table or a bookshelf. A dining table needs to be sturdy and durable enough to withstand the daily use and abuse it’s likely to see over its lifetime. Therefore, you must consider strength as well as beauty. Choosing a dense hardwood, although more expensive, will produce a table that will withstand a lot of abuse and end up being a better choice overall.
Now you must choose the color and grain of the species. This is largely going to come down to personal taste and aesthetics but there are a few other things to keep in mind. Certain woods, such as Oak and Ash, will give your new table a very different finished look than a species such as Cherry or Walnut. The workability of your new material is just as important. At this point, you have a design, and you know what joinery you will need to cut. That beautiful grain you love so much may become your worst enemy later as you tackle a specific joint or process in the project. If you’re a seasoned woodworker, you may revel in the challenge but for a novice, it can quickly become discouraging and quite possibly become a huge roadblock to the success of your project.
Things are moving along nicely, you have your design, and you’ve chosen your wood species. You’ve given thought to the joinery, grain, color, and wood movement, and how all these factors will affect your new table. Now, where do you get this stuff? Where you are located is going to be the biggest factor in what is available to you. It will also be the biggest factor in what sets the cost. Areas with a lot of access to raw materials will, for obvious reasons, have a large supply of materials at a lower price. The opposite is true for areas where wood is scarcer. Search the internet for “hardwood supplier” in your area. You will soon find the suppliers that have the goods you’re after. Go down and look at what each supplier has to offer. Familiarize yourself with their stock and how they are to deal with. Some will let you pick through the pile and get those special boards your after. Others will not. I’d suggest if they won’t let you choose your material then leave. Head to another supplier and invest the time needed to get the best material you can afford. The amount of time you’ll spend crafting your new table will be substantial. Spending that time struggling with expensive, subpar material will, for sure, be an unpleasant experience.
While you are at your lumber supplier take the time to look around at the other offerings they have. Check out not only the hardwoods but the softwoods and sheet goods they have on hand. Many suppliers have an overwhelming array of choices and will leave your head spinning with all the possibilities for your current and upcoming projects. The turnover for lumber can be high at times and that beautiful wood you see there today may very well be gone tomorrow so remember when you find that wood you just have to have “Buy as much as you can reasonably afford, then just a little more”.
One last point I’d like to touch on is finishing. As woodworkers, we must learn to choose and apply appropriate finishes to our projects. This can be a rewarding experience or a disaster. Like wood movement, the more you learn about this aspect of the craft the better you’ll be at choosing appropriate woods for your projects. “Understanding Wood Finishing” by Bob Flexner, another college textbook, has been a valuable resource over the years. “Finishing” by Jeff Jewitt is another great resource. Of course, the endless information online and communities you can participate in will go a long way in educating yourself about this aspect of the craft.
As you can see there are a lot of factors to consider when choosing your materials. Above is simply a starting point to get you rolling and keep you on track, but the learning will be endless and lifelong. That’s the beauty of learning and mastering any craft. It’s the journey and all the wonderful things you’ll be able to imagine, then craft, with your own two hands. The people you’ll meet along the way and ultimately the joy you’ll feel when you stand back and look at that newly crafted masterpiece.
Have fun, be careful, and remember “Make it Or Die Trying.